International Armoured Vehicles 2021: Technology Demonstrator 6 Update
The UK Ministry of Defence’s Defence Science and Technology Laboratory held a presentation during International Armoured Vehicles 2021, providing updates on the Dstl’s Technology Demonstrator 6 hybrid electric drive project.
The presentation laid out the goals of Technology Demonstrator 6, which are to demonstrate the benefits of hybrid electric drive that can be delivered to the battlefield today, using demonstrators of vehicles currently in service with the British military converted to hybrid electric drive. The MAN SV, Jackal and Foxhound demonstrators will be trialed to compare their performance and fuel efficiency with their conventional counterparts, in addition to exploring other benefits such as exporting power or battery-only operation. Dstl says that the trials will allow the definition of “achievable and meaningful requirements” for hybrid electric drive platforms going forwards.
The three demonstrators all use differing hybrid electric drive configurations. The MAN SV uses twin electric motors driving propshafts to the front and rear axles of the truck, while Foxhound uses four in-hub electric motors. The Jackal uses four inbound electric motors instead, with Dstl stating that the differing configurations for Foxhound and Jackal will allow for a “good feel” of their comparative advantages and disadvantages.
While the Foxhound and Jackal demonstrators are still under final assembly and are planned for delivery at the end of this month for trials beginning in March, the MAN SV demonstrator has already been delivered to Millbrook. Testing of the MAN SV is already underway, with its drivers saying that it is much easier to drive than a normal truck due to increased torque and lack of gear changes. According to the speaker, the testing included a drag race against a conventional MAN SV uphill to test the performance benefits. The MAN SV demonstrator is planned to start chamber testing in April 2021. A stakeholder day is planned for June 2021, and the final report will be made in October 2021.
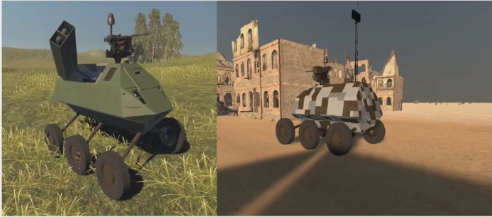
Dstl also showed off some of its concepts for its Future Ground Combat System research project. The FGCS project hypothesizes that exploiting emerging technologies like active protection systems, “active stealth”, advanced mobility and unmanned systems can reduce reliance on heavy armor, enabling light yet survivable vehicles. These lighter vehicles can be wheeled, and provide increased operational mobility and efficiency compared to a tracked vehicle. In particular, Dstl is looking into whether individual wheel torque control and other technologies facilitated by electric drive can “close the gap” between wheeled and tracked vehicles’ terrain accessibility, describing the project as exploring the “art of the possible”.
Dstl’s current research for FGCS involves developing light (15 tons), medium (30-40 tons) and heavy vehicle concepts, with these concepts undergoing synthetic environment trials to assess their survivability and utility. In particular, Dstl highlighted their collaboration with Prodrive into a novel suspension concept that offers the ability to change track width and ride height on demand, allowing for a wheeled vehicle using the suspension concept to enjoy off-road mobility and blast protection comparable to a larger vehicle while remaining able to fit in an ISO container.
FGCS is part of Dstl’s work to explore future platforms that in addition to fully exploiting the efficiency and capability benefits of electric drive, also support a future migration from hybrid-electric to all-electric propulsion. It is hoped that exploitation of these technologies will provide “highly efficient, deployable and agile” platforms that meet the requirements of the Ministry of Defense’s Integrated Operation Concept.
Dstl noted that the problem of long ranges and recharging batteries in the field drove the decision to currently focus on hybrid electric drive, as it was estimated that an all-electric main battle tank would require 50 tons of batteries to reach a range of 200 kilometers, while implementing a electric crossdrive transmission would provide immediate efficiency and reliability benefits. The speaker also commented on the need to evaluate electric propulsion systems on more metrics like response times and recharge times instead of just energy density, even as energy density is projected to improve in the future.